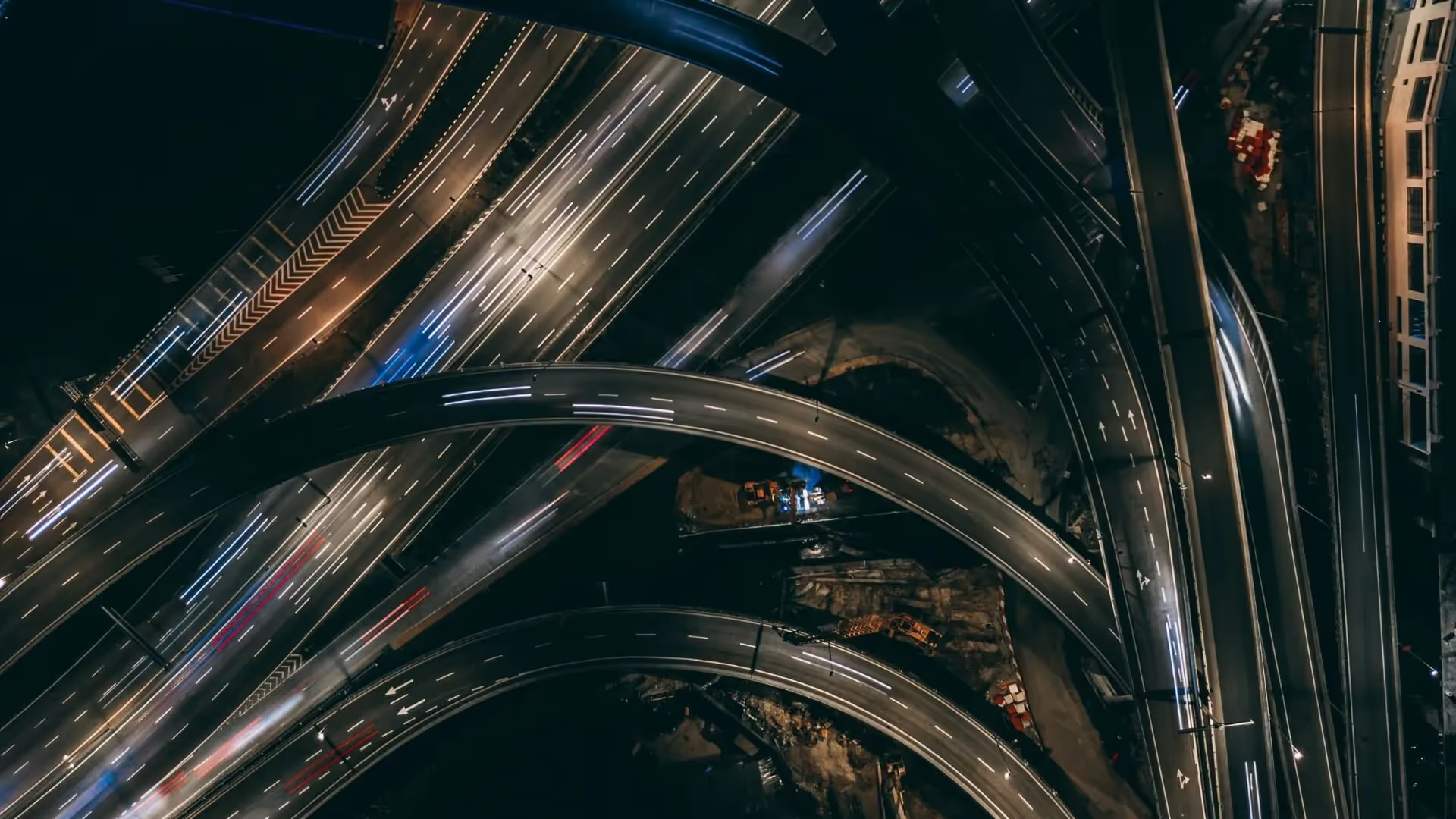
A supply chain runs on such a razor-thin margin for error that a single point of failure can have catastrophic and far-reaching consequences. If you doubt this, consider the Suez Canal blockage back in March 2022, which cost some companies an astonishing $400 million per hour; that’s over $9 billion a day in lost revenue just over this one ship in this one major shipping channel.
While companies may not be able to physically move container ships like this one out of the way to unblock supply chains, it offers a valuable lesson. When there are events you cannot control, it is that much more vital to control the events that you can. Increasing visibility beyond Tier 1 providers, or direct suppliers of the final product, will ensure companies can control what’s in their power and pivot quickly to mitigate what they can’t.
Leveraging structural visibility
Structural visibility is a traditional concept with a more limited scope, but that doesn’t mean it isn’t relevant. It lets companies know where their suppliers are and how these interrelationships affect fulfillment. Companies typically leverage data in two distinct ways for visibility into their supply chain infrastructure.
Engaging in traditional inquiry
Companies can improve structural visibility by consistently engaging in traditional inquiry types throughout the supply chain life cycle. These inquiry types include network mapping, risk management, and modeling.
Data from cargo locations, as well as costs related to the transport of key cargo and materials, are typical metrics. Companies must also monitor supply chain activities such as order receipts, bills of lading, and proof of delivery. Auditing records can also supply vital information for visibility.
The challenge is consistent, accurate documentation. Throughout traditional record keeping, many supply chains rely on manual processes, which are fraught with human error. Missing and incorrect information due to a lack of automatic documentation can prevent companies from understanding where and why bottlenecks and obstacles keep appearing.
Implementing new techniques like digital twins
Some companies are using new methods such as digital twin technology to explore the impact of different scenarios and disruptions. They create a virtual replica, or digital twin, of their supply chain and operations and use this virtual environment to test for vulnerabilities and weaknesses. This gives companies greater insight into hypothetical scenarios—both optimized conditions and worst-case scenarios—so that they know how the supply chain could perform under these changes.
Digital twins and other technologies such as these are data- and processing-heavy tools. The supply chain will need a dashboard that can integrate the information from all these tools into a single point of view as well as continually supply high-quality data to power the solution.
Leveraging dynamic visibility
Structural visibility may provide a close look into conditions as they were in the past, but dynamic visibility tells supply chain companies where their operations stand right now. With dynamic visibility, companies can respond in real-time to events and pivot more quickly to mitigate any consequences of disruption.
The challenge in achieving this comes in several layers:
- Data access: Dynamic visibility requires real-time data access, something many companies aren’t prepared for thanks to traditional, gated governance strategies. In addition, many solutions require heavy IT oversight, which slows down insights.
- Data processing: Companies need advanced technologies such as machine learning and other artificial intelligence methods to find patterns and move to a proactive response to events, but these solutions require a high volume of high-quality data.
- Automation: Too many manual processes slow the path to insights by leaving out crucial information or allowing human error to skew final results.
- Collaboration: Having too many data silos prevents supply chain vendors, departments, and teams from collaborating to increase accuracy and respond to disruption.
For structural and dynamic visibility to work, the supply chain will need a new solution that doesn’t just increase visibility but successfully shifts companies from a reactive state of operations to a proactive one.
Using a data operating system as a supply chain control tower
The supply chain is only becoming more complex as companies move toward a flexible, decentralized model. The supply chain control tower should offer predictive capabilities and increase automation.
A data operating system unites all frameworks and tools within the supply chain ecosystem. It creates a single source of truth that improves documentation and reporting and allows decision-makers to see what data is available and all dependencies.
In addition, it allows all team members access to the data they need to make real-time decisions while ensuring only high-quality data powers next-gen tools such as machine learning models and digital twin deployments.
The Modern Data Company created the world’s first data operating system, DataOS,to democratize data for everyone. It allows even nontechnical users to build the models they need for complete structural and dynamic visibility into the entire supply chain and monitor what’s happening in real-time.
DataOS encourages collaboration, provides complete governance while ensuring security, and ensures that companies can finally use the data they’ve gathered, regardless of source or format. It’s the perfect partner for a rapidly changing supply chain and is the simplest way to get data under control with minimal operational disruption.
To find out more about how DataOS can change how you approach visibility within your supply chain.